by Rob Sinfield, VP Product, Sage
Supply chain shortages, inflation and economic pressures have been cited as some of the key macro-economic challenges facing the manufacturing sector in 2023. However, one of the most pressing issues is the unresolved issue of labour and talent shortage. Nearly 4 in 5 employers globally have reported difficulty in finding the skilled talent they need in 2023, which is increasing on average by 2% year over year. This is having a real impact on not only individual organisations but the economy as a whole.
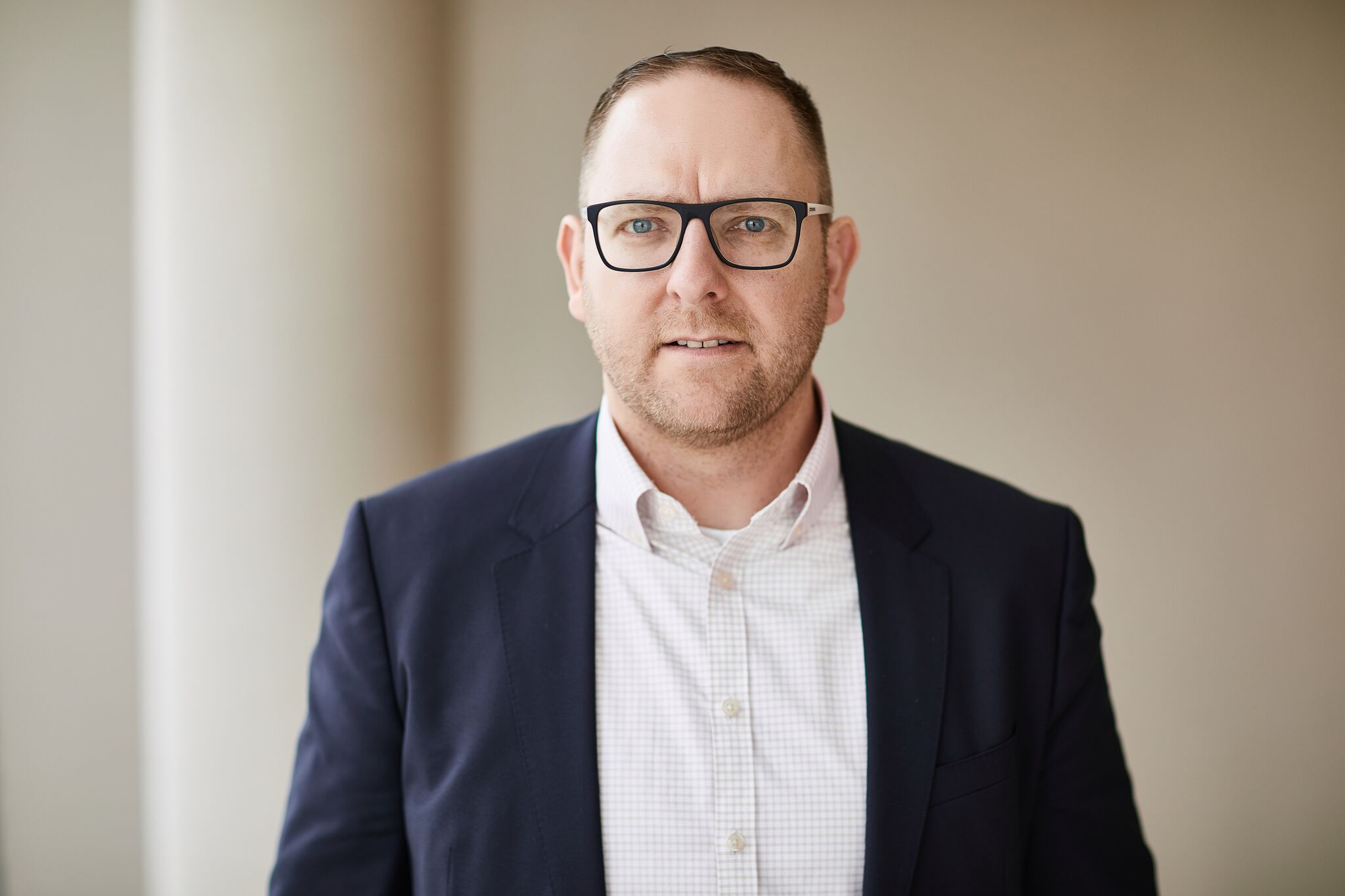
For example, in South Africa, the FoodBev Sector Education and Training Authority found that of the 633 organisations in the sector, about 43% of them cited a lack of skilled people as a major reason they could not fill vacancies, while a further 27% cited an inadequate supply of suitable candidates.
So, what can be done to fill the void?
Technology is challenging what manufacturers do, from robotics and 3D printing, to data, cyber security, and remote working. But its capabilities in solving the talent crisis are not being fully realised.
Cloud investment for more flexible working
Cloud has become incredibly important for streamlining processes, increasing efficiencies, and unlocking new opportunities for growth in manufacturing and is therefore one of the top areas of investment for manufacturers. Many believed that Cloud spending in Africa would die down in the wake of the massive adoption that took place in 2020 and 2021. According to the “Cloud in Africa 2023” study released by World Wide Worx, it found that 69% of organisations expect to see an increase in cloud spend, and only 7% expect spending to decrease, as reported by Connecting Africa.
Cloud technology has the ability to improve data management whilst requiring little investment or expertise, and cloud-based applications have the ability to return high-cost savings whilst needing little maintenance. For example, they are often able to be automatically refreshed and updated by the vendor, instead of forcing an IT department to perform manual organisation-wide updates. And by providing manufacturers access to valuable data, they are able to identify patterns, optimise processes, and make more informed decisions about the impact of business operations. For example, ERP software can benefit production by allowing manufacturers to match production levels to sales data and stock levels, and the system can manage pricing and orders and reduce mistakes, leading to a more efficient process and reduced order cycle times.
From a talent shortage perspective, cloud technology improves business productivity, meaning organisations have more cash available to offer competitive payrates and a more satisfying work environment that is varied and smooth. And, what’s more, in the world of hybrid working, it enables manufacturers to offer remote working as an option. While there was previously a perception that manufacturers needed to operate on-premise in order to succeed, the pandemic proved that to be false. Thanks to cloud technology, recent research suggests 63% of manufacturing organisations now have a hybrid working programme in place which is not only an attractive pull to people entering the workforce but also allows employers to recruit from a wider talent pool.
Adopting a cloud solution or cloud technologies needs to be considered as part of a digital transformation strategy. And, manufacturers don’t need to change all the solutions at once; they can select those that they want to replace and do this incrementally. A big bang approach, although often beneficial, does not necessarily guarantee immediate benefits. Selecting the right areas of your technology ecosystem to move to the cloud will help with change management and the successful adoption of new tools and ways of working.
Building a circular economy
From a talent retention perspective, technology also has a role to play in creating a more attractive and sustainable work environment. Aside from meeting environmental, social, and governance (ESG) targets and making operational and equipment efficiencies, companies that demonstrate their green credentials are appealing to both the more conscious buyer and job candidate. According to a global study, 68% of people are more willing to accept positions from companies that are environmentally sustainable, meaning organisations that fail to innovate risk being rejected by top talent.
As the world approaches the halfway point of the 2030 UN and COP Agenda, new sustainability targets are being set, making the issue ever more pressing. The SME Climate Impact Report, commissionedby Sage in partnership with Oxford Economics and the International Chamber of Commerce (ICC), and launched at COP27, cited that reducing waste (46%) and energy use (42%) are among the most common steps SMEs are taking to reduce their environmental footprint.
As a result, more manufacturers need to start looking at the circular economy, from reducing waste to repurposing materials and products. By looking at operational and equipment efficiencies, there are ways to increase the lifespan of machinery and products to make cost savings. Research suggests that 32% of manufacturers who have invested in the Circular Economy can see benefits to adopting this strategy, and IoT, Machine Learning, and Artificial Intelligence will be key to this approach, ensuring organisations have the right data to make informed decisions.
One top tip for manufacturers looking to start or enhance their circular economy and ESG journey is to prioritise collaboration and partnerships. Why is this so important? It allows companies embarking on adopting circular economy principles to learn from these organisations. This might entail partnering with NGOs or universities. Another tip is looking at circular supply chains to optimise material flows, reduce waste and improve how you utilise resources.
The perception challenge
The final area that manufacturing needs to target is a perception issue. Contrary to its historical reputation, manufacturing today is a highly skilled and specialised sector, fulfilled in clean and modern environments. Often, people are unclear about the role of technology in manufacturing and think that at some point they will be replaced in their role by a robot or automation, exacerbating a perception that manufacturing is not an attractive career choice.
However, as AI, robotics and cloud computing become an integral part of the job description, manufacturers can set themselves apart from other industries and position themselves as compelling and exciting environments where there is potential to learn new skills. AI and robotics, in particular, reduce heavily manual and laborious processes, freeing up time to spend on more high-value tasks.
Changing the image of manufacturing will be key to attracting a new and diverse group of potential employees. For example, there is a need for the sector to open up the application pool, reforming and encouraging apprenticeship schemes, not just for people at the start of their careers but for all ages and backgrounds. With proper training, manufacturing can set itself apart as a sector that is able to kickstart an exciting, future-proofed and accessible career for any individual.
The modern manufacturer is far from the images depicted of manufacturing in the industrial revolution. Changing perceptions of modern manufacturing to highlight its significant differences from well over 100 years ago requires a comprehensive approach that focuses on communication, education, and showcasing the advancements and positive impacts of the industry. Showcasing how technology is changing manufacturing through automation is just one way of altering this perception for the better. Bringing sustainability and circularity to the forefront will help to change consumer and local community perceptions. Why not showcase products and innovation through social media and other digital platforms to help highlight that there is a future for highly skilled labour?
There is a great opportunity facing the manufacturing sector right now – and filling the skills gap will require refocussing on what the new pipeline of talent could look like beyond traditional recruitment and reskilling methods and harnessing the power of technology like never before. Making a concerted effort to support the need for hybrid working to attract a new talent pool and adopting AI and machine learning technologies to minimise time-intensive repetitive tasks, will be key to taking the sector in a new direction that offers an attractive career and is at the forefront of emerging technologies.